Feature article
The benefits of opting for a prefab home
When the option exists to reduce the cost of building, why wouldn’t you consider a prefab home?
Last updated: 29 May 2024
With a general build time of around 10–12 months — including planning and consenting — and an average build cost of anywhere from $4000–$6000 per square metre for a traditional build, it’s not surprising that many Kiwi are looking at alternatives for building their family home.
One such alternative that is quickly gaining traction is prefabrication. While in the past, most prefab buildings have been fairly utilitarian, modern prefab homes have all the amenity of traditionally built homes. Not only that, but thanks to some significant R&D into the subject, the number of prefab home designs available means you can have just about any style of home you want — from ‘space age’ prefab dome houses to upcycled container houses and even prefabricated houses with a ‘Hamptons’ or ‘Scandinavian’ chic.
These three prefab homes illustrate the breadth of design sophistication contemporary prefabrication can achieve.
1. Glacial Retreat by Nott Architects
Image: Marina Mathews
This prefabricated house designed by Nott Architects was built off site and delivered to the remote site by truck in four loads.
On a remote station about halfway between Aoraki Mt Cook and Timaru, near Lake Tekapo, this house was designed to settle effortlessly into a harsh landscape of snow and storms, and long, dry summers.
Wrapped around a rock, this house of pavilions, designed by architect Charlie Nott of Nott Architects, was prefabricated off site and trucked to its final destination in four pieces.
Trucking the house to site meant various design restrictions, with the maximum dimensions for each load around 6 metres by 22 metres; the final design comprised four separate ‘parts’ to allow for this. “Remote locations like this are often problematic with weather, and getting people and materials to site. By designing prefabricated homes for rural and remote sites, we are trying to reinvent the perception of what a relocatable house can be, and I think here we have proved that a well-designed prefabricated home can be a huge success,” Charlie says. Read more about Glacial Retreat.
2. Brooklyn Mini FAB by Bonnifait + Associates
Floating in the trees on a Wellington hillside, the 2024 Small Home of the Year, Brooklyn Mini FAB by Bonnifait + Associates is part of the architect’s FAB series of prefab homes, designed with modulation and affordability at heart.
Brooklyn Mini FAB was named the 2024 Small Home of the Year. With exceptional commitment to affordability and repeatability through prefabrication, Mini FAB exemplifies the architect’s commitment to providing housing solutions for small-scale living in under-used and difficult sites.
A mere 37 square metres, Mini FAB embodies innovation, sustainability, and functionality in a compact footprint. Nestled against the verdant hills of a Wellington valley, this perky little house exudes energy and charm, offering a modern sanctuary amidst nature’s embrace. Despite its modest floor area, the inclusion of a narrow mezzanine bedroom over a double-height space generates spatial energy, maximising every inch of available room.
3. Makespace
This architecturally designed prefab home by Makespace, a New Zealand company that designs and delivers prefabricated baches and dwellings to hard-to-reach and remote sites, is a sophisticated example of contemporary prefab design.
Mostly, these little homes are tucked away in extremely remote locations, but within their small footprints are spaces where the living is large and the connection to the vast landscapes surrounding them is undeniable. They’re architecturally designed modular baches, crafted in Auckland and Christchurch and delivered to hard-to-access sites around New Zealand. They’re the brainchild of Isaac Lindesay who founded Makespace in 2020 with the aim of developing sophisticated modular buildings, reducing waste and achieving cost and time efficiency.
So why prefab? Here are some more reasons why you should seriously consider going prefab with your next home.
Factory built vs onsite construction
Building in a factory means the usual weather considerations are null and void. While inclement weather isn’t too much of a worry for framing materials, other materials, such as flooring and wall linings, can be negatively impacted by bad weather. Similarly, building in a factory means construction itself isn’t hampered if the weather outside is less than stellar.
A further advantage to factory-built homes is that because they need to be moved to site, they often have additional bracing or have steel framing, to withstand the rigours of transportation, which results in a more robust build.
Cost savings are myriad
When building, it’s not just the build costs that need to be factored in, but all the associated costs as well. Since prefabricated house companies can build multiple homes at once, they tend to buy and store their materials in bulk, which means they can pass these lower material costs on to you. This also means such companies are able to offer you a true, fixed-price contract. Traditional onsite construction may also have added costs, particularly if you’re building rurally, as your builder may factor in travel costs for the build team.
Also, most prefabricated homes are designed to sit on pile foundations, rather than concrete slabs, which means you can save money by utilising ground screws, which have the added benefits of being faster to install and environmentally friendly.
Eco prefab homes
As mentioned, the use of a ground screw foundation, not only means a faster install but also up to 60 per cent less carbon emissions during manufacture than the comparable concrete products for the same foundation.
Likewise, waste is a big concern in construction. So, it’s good news then that prefabrication companies utilise a ‘lean manufacturing process’. This means that through the systemisation of production, prefabrication manufacturers are able to reduce the amount of waste and other by-products from the building process going to landfill — a positive impact on our environment, as well as the bottom line.
So, if you’re looking to build, take a closer look at one of the many local prefabrication options available.
Author
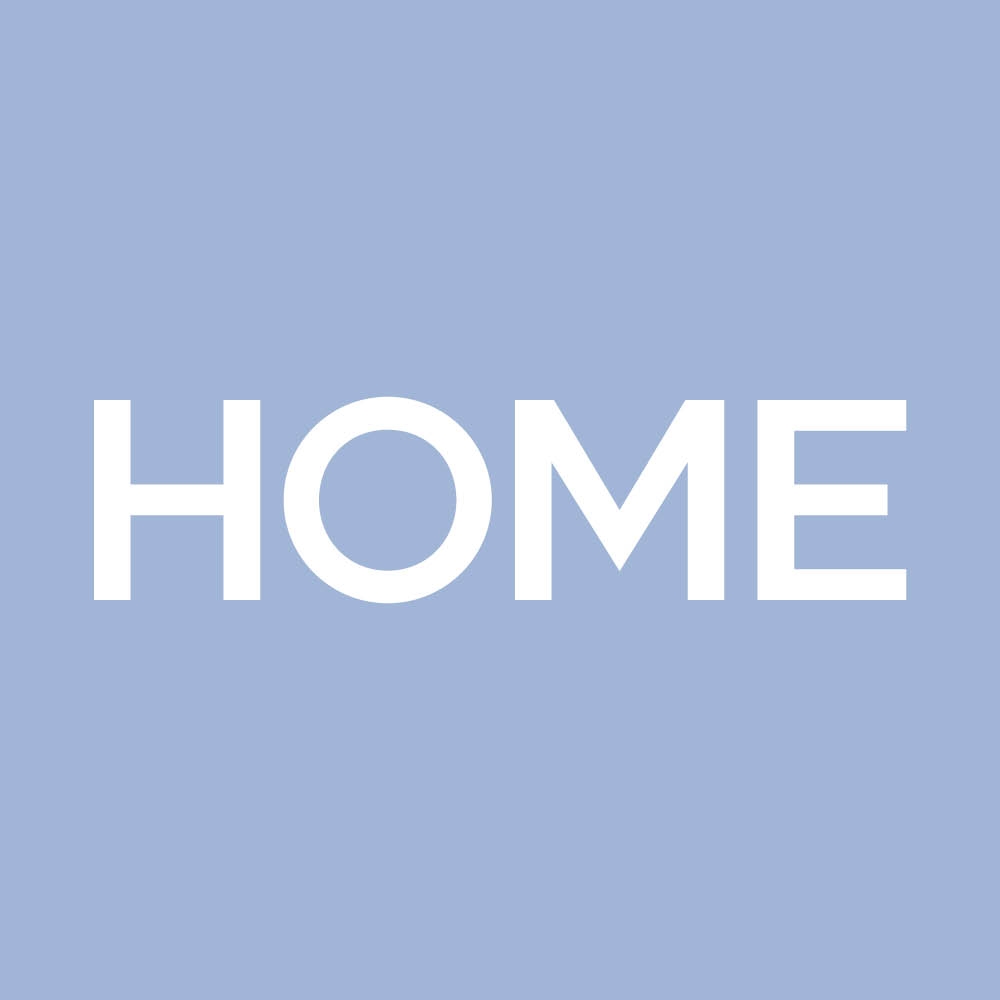
Other articles you might like